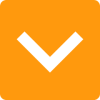
Ed Vergunst (54) is sinds 2015 werkzaam bij de Eerste Nederlandse Cement Industrie (ENCI), een bedrijf dat onderdeel is van de Duitse multinational Heidelberg Materials. Met twee producerende fabrieken in Rotterdam en IJmuiden speelt ENCI een belangrijke rol in de cementindustrie. Ed begon zijn carrière als leerling operator en groeide door tot productiemanager, waarbij hij verantwoordelijk is voor het leveren van hoogwaardige cementproducten.
ED VERGUNST: EEN KIJKJE IN DE WERELD
VAN DE CEMENT-INDUSTRIE
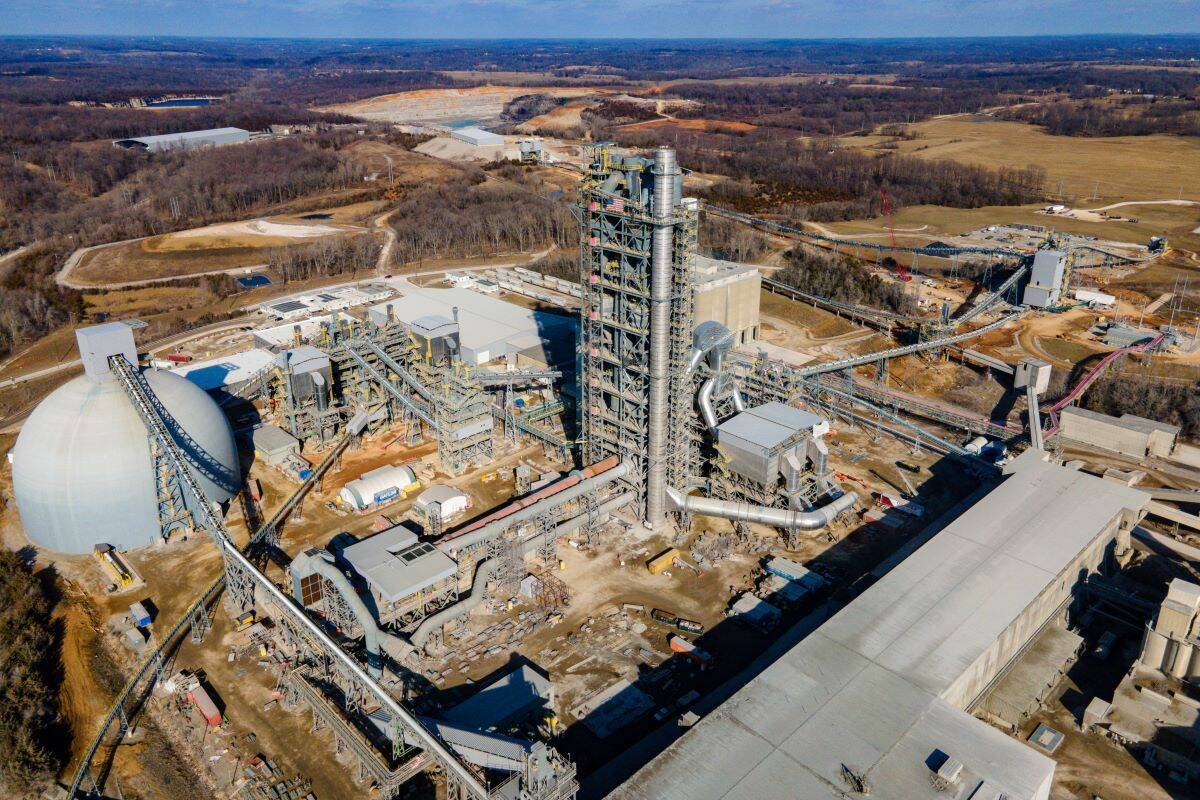
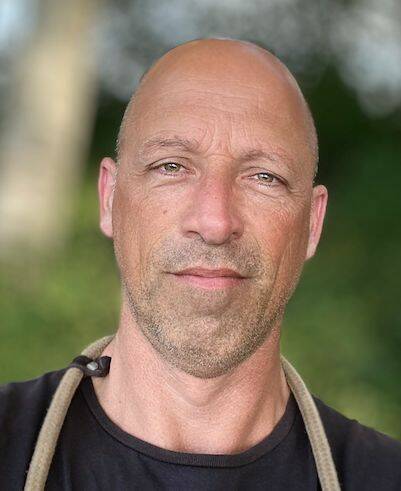
LEES OOK DE ANDERE VERHALEN
VAN DE PRODUCTIE SECTOR
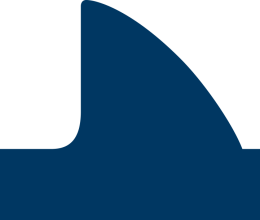
HOE WERKEN JULLIE DAGELIJKS AAN EEN VEILIGE WERKOMGEVING?
Veiligheid staat centraal bij ENCI. Er worden continu maatregelen genomen om een veilige werkomgeving te creëren. Medewerkers worden hier regelmatig op aangesproken en er zijn systemen om onveilige situaties te melden. ‘Er staan hier hele grote machines en het is grof werk. We spreken onze mensen dan ook voortdurend aan op veiligheid. Deze week hebben we een safety week, waarbij we allerlei safety issues de revue laten passeren. Wat ik vooral steeds probeer uit te dragen, is dat iedereen ‘stop’ kan zeggen op elk moment. Als een medewerker zich niet veilig voelt in een situatie of hij merkt een onveilige situatie op, dan moet hij stoppen en niet toch nog even gaan kijken. Dat is vooral wat ik, maar ook de plantmanager en de anderen uit willen dragen: “Je doet het veilig of je doet het niet”.
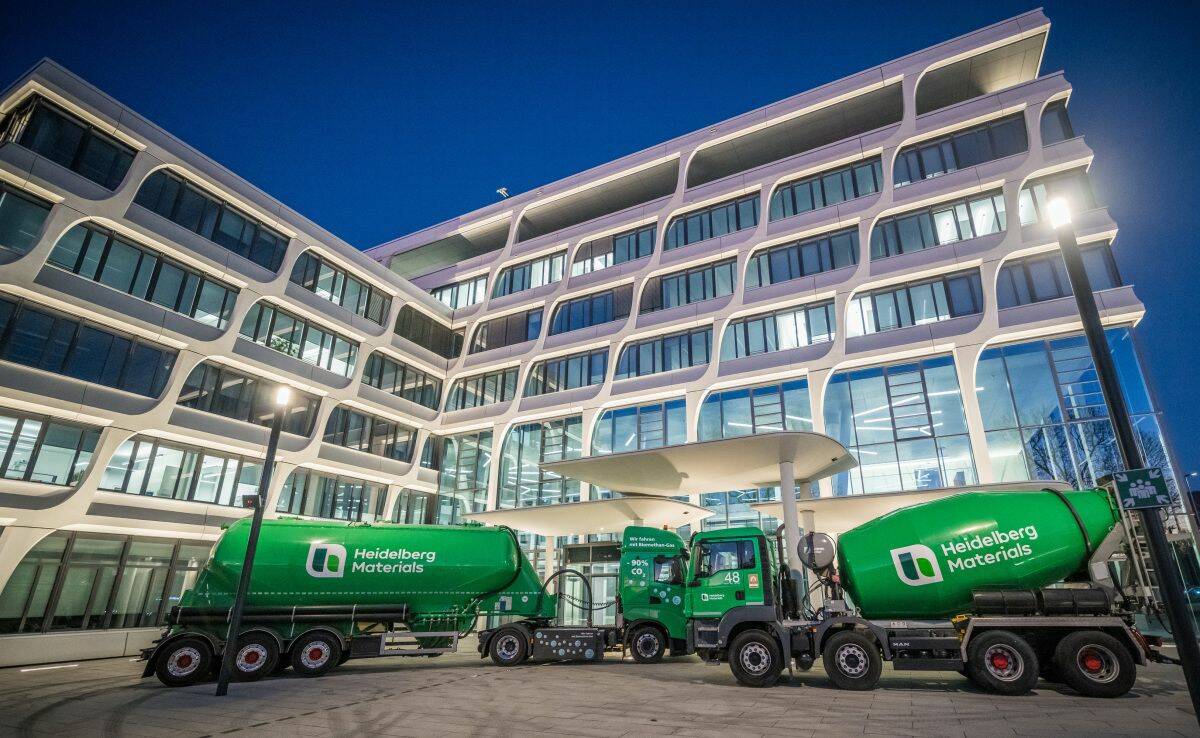
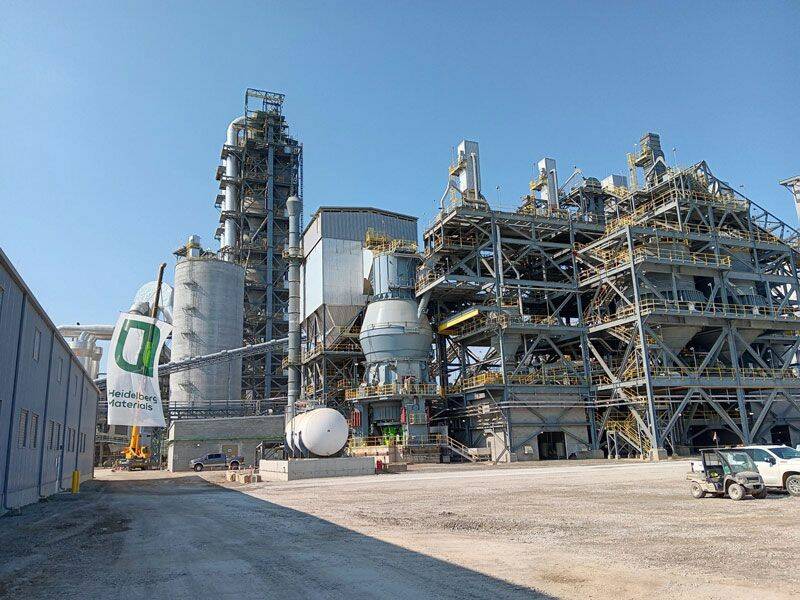
WELKE ONTWIKKELINGEN VOORZIE JE DE KOMENDE JAREN M.B.T. HET PRODUCT DAT ENCI MAAKT?
Heidelberg Materials, het moederbedrijf van ENCI, richt zich op duurzaamheid en klimaatneutraliteit. ENCI werkt ook aan het verminderen van CO₂-uitstoot en onderzoekt mogelijkheden voor energiebesparing en duurzame grondstoffen. Hoewel het proces zelf volgens Ed sinds 1965 niet veel is veranderd, wordt er wel gekeken naar optimalisaties op het gebied van duurzaamheid. ‘Hier staat nog steeds dezelfde molen, maar de apparatuur is uiteraard wel gemoderniseerd. Zo kunnen we nu veel nauwkeuriger de grondstoffen wegen. Maar het maalproces zelf, daar verandert op zich niks aan. Wat betreft grondstoffen is er veel aandacht voor duurzaamheid en is Heidelberg op zoek naar alternatieven voor de productie van cement. Het produceren van onze grondstoffen veroorzaakt grote hoeveelheden CO₂-emissie. Zo kijken we naar verschillende grondstoffen, waar de CO₂-footprint al is verlaagd door onze leveranciers. Ook onze drogerij verbruikt gas; als het materiaal wat erin gaat droger is, dan hebben we minder gas nodig. We zoeken op die manier altijd naar een betere balans, hoe we als kleine fabriek ook een bijdrage kunnen leveren op het gebied van sustainability.’
HOE ZORG JE ER DAGELIJKS VOOR MET JE TEAM DAT DE PRODUCTIEDOELEN WORDEN BEHAALD?
ENCI streeft ernaar om wekelijks voldoende cement te produceren om aan de vraag te voldoen. De productiedoelen zijn afhankelijk van de verzending die plaatsvindt. Hoewel de bouwsector momenteel wat vertraagd is, maakt ENCI nog steeds voldoende cement voor verschillende toepassingen zoals wegenbouw en tunnels. Ed: ‘We hebben hier twaalf silo’s staan, een voorraad van ca. 14.000 ton en het is de bedoeling dat iedere week de silo's vol zijn voor de week erna. Onze productiedoelstellingen zijn geheel afhankelijk van de verzending die per week plaatsvindt. Ik heb ‘s morgensvroeg overleg met de assistent productie en de technische dienst. Dan kijken we naar wat er aan storingen is gemeld en daarna ga ik of de assistent de controlekamer in en bespreken we met de collega’s de productie voor die dag. De teamcoördinator bepaalt wie waar welke werkzaamheden gaat doen. Dat is elke dag weer anders. Beginnende operators zitten vaak op dezelfde plek, omdat ze het werk daar eerst moeten leren, maar allround operators kun je overal tegenkomen.’
WAT KAN JE OVER ENCI VERTELLEN?
In 1964 bouwde ENCI een fabriek in het Botlekgebied in Rotterdam voor de productie van hoogovencement. Dit is een speciaal type cement. In IJmuiden staat, naast de hoogovens, ook een cementfabriek. In de fabriek in Rotterdam worden grondstoffen per schip aangeleverd. Na toevoeging en droging van onder andere hoogovenslak wordt hier cement van gemalen. ‘Toen de fabriek in de Botlek werd gebouwd was het ook de bedoeling om hier een gedeelte van de hoogovens neer te zetten, maar dat is nooit gebeurd. Onze grondstoffen komen allemaal via het water per schip. Wij maken heel veel cement, 500 kiloton (kt) per jaar, in vier verschillende cementsoorten. Er staan twee grote kogelmolens, een van 14,5 meter lang bij een doorsnee van 4,5 meter en een “kleinere” van 12 meter en 4 meter doorsnede waar de grondstoffen ingaan. De kogels erin zorgen voor het malen. Het gewicht van de stalen kogels van de grote molen alleen al is 288.000 kilo. Het zijn dus gigantische machines, om een beeld te schetsen.’
Op de vraag naar een omschrijving van de cultuur bij ENCI, antwoordt Ed: ‘We zijn een hele kleine organisatie, zo’n veertig man personeel hebben we hier op de plant. Iedereen zit in het hoofdgebouw, dus je hebt veel contact met elkaar. We zijn op elkaar aangewezen en doen alle voorkomende werkzaamheden. Bij productie werken we met een 5-ploegendienst. Deze teams bestaan uit vier operators en er zijn ook twee ploegendiensten die op de kade lopen. Zij zorgen voor het aanleveren en het afvoeren van materiaal.’
Ed begon bij ENCI als leerling operator en groeide door in de organisatie tot allround operator en teamcoördinator, sinds vorig jaar februari is hij productiemanager. ‘Het proces is niet heel ingewikkeld, er komen wel veel werkzaamheden bij kijken die allemaal worden uitgevoerd door onze operators. Dat is nou precies wat ons proces zo interessant maakt.’ We duiken met Ed in de wereld van cement en praten over wat er allemaal komt kijken bij het productieproces.
ED VERGUNST: EEN KIJKJE IN DE WERELD
VAN DE CEMENT-INDUSTRIE
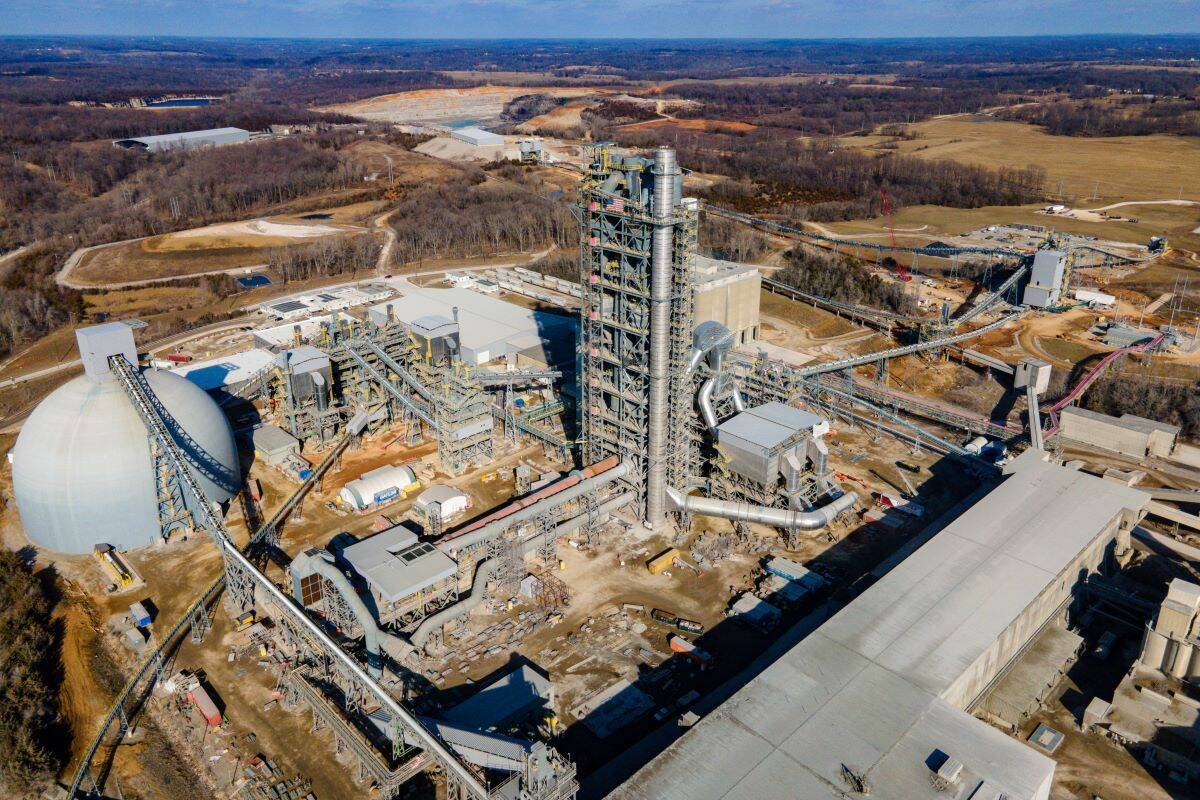
HOE WERKEN JULLIE DAGELIJKS AAN EEN VEILIGE WERKOMGEVING?
Veiligheid staat centraal bij ENCI. Er worden continu maatregelen genomen om een veilige werkomgeving te creëren. Medewerkers worden hier regelmatig op aangesproken en er zijn systemen om onveilige situaties te melden. ‘Er staan hier hele grote machines en het is grof werk. We spreken onze mensen dan ook voortdurend aan op veiligheid. Deze week hebben we een safety week, waarbij we allerlei safety issues de revue laten passeren. Wat ik vooral steeds probeer uit te dragen, is dat iedereen ‘stop’ kan zeggen op elk moment. Als een medewerker zich niet veilig voelt in een situatie of hij merkt een onveilige situatie op, dan moet hij stoppen en niet toch nog even gaan kijken. Dat is vooral wat ik, maar ook de plantmanager en de anderen uit willen dragen: “Je doet het veilig of je doet het niet”.
WELKE ONTWIKKELINGEN VOORZIE JE DE KOMENDE JAREN M.B.T. HET PRODUCT DAT ENCI MAAKT?
Heidelberg Materials, het moederbedrijf van ENCI, richt zich op duurzaamheid en klimaatneutraliteit. ENCI werkt ook aan het verminderen van CO₂-uitstoot en onderzoekt mogelijkheden voor energiebesparing en duurzame grondstoffen. Hoewel het proces zelf volgens Ed sinds 1965 niet veel is veranderd, wordt er wel gekeken naar optimalisaties op het gebied van duurzaamheid. ‘Hier staat nog steeds dezelfde molen, maar de apparatuur is uiteraard wel gemoderniseerd. Zo kunnen we nu veel nauwkeuriger de grondstoffen wegen. Maar het maalproces zelf, daar verandert op zich niks aan. Wat betreft grondstoffen is er veel aandacht voor duurzaamheid en is Heidelberg op zoek naar alternatieven voor de productie van cement. Het produceren van onze grondstoffen veroorzaakt grote hoeveelheden CO₂-emissie. Zo kijken we naar verschillende grondstoffen, waar de CO₂-footprint al is verlaagd door onze leveranciers. Ook onze drogerij verbruikt gas; als het materiaal wat erin gaat droger is, dan hebben we minder gas nodig. We zoeken op die manier altijd naar een betere balans, hoe we als kleine fabriek ook een bijdrage kunnen leveren op het gebied van sustainability.’
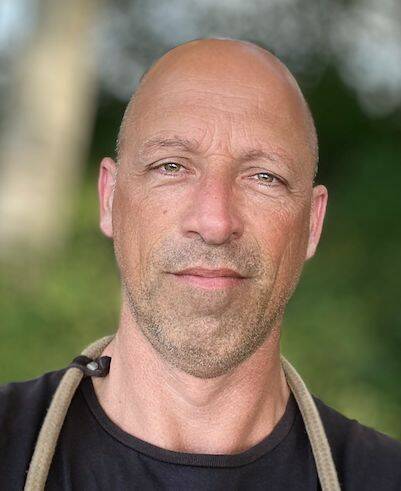
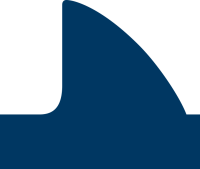
LEES OOK DE ANDERE VERHALEN
VAN DE PRODUCTIE SECTOR
WAT KAN JE OVER ENCI VERTELLEN?
In 1964 bouwde ENCI een fabriek in het Botlekgebied in Rotterdam voor de productie van hoogovencement. Dit is een speciaal type cement. In IJmuiden staat, naast de hoogovens, ook een cementfabriek. In de fabriek in Rotterdam worden grondstoffen per schip aangeleverd. Na toevoeging en droging van onder andere hoogovenslak wordt hier cement van gemalen. ‘Toen de fabriek in de Botlek werd gebouwd was het ook de bedoeling om hier een gedeelte van de hoogovens neer te zetten, maar dat is nooit gebeurd. Onze grondstoffen komen allemaal via het water per schip. Wij maken heel veel cement, 500 kiloton (kt) per jaar, in vier verschillende cementsoorten. Er staan twee grote kogelmolens, een van 14,5 meter lang bij een doorsnee van 4,5 meter en een “kleinere” van 12 meter en 4 meter doorsnede waar de grondstoffen ingaan. De kogels erin zorgen voor het malen. Het gewicht van de stalen kogels van de grote molen alleen al is 288.000 kilo. Het zijn dus gigantische machines, om een beeld te schetsen.’
Op de vraag naar een omschrijving van de cultuur bij ENCI, antwoordt Ed: ‘We zijn een hele kleine organisatie, zo’n veertig man personeel hebben we hier op de plant. Iedereen zit in het hoofdgebouw, dus je hebt veel contact met elkaar. We zijn op elkaar aangewezen en doen alle voorkomende werkzaamheden. Bij productie werken we met een 5-ploegendienst. Deze teams bestaan uit vier operators en er zijn ook twee ploegendiensten die op de kade lopen. Zij zorgen voor het aanleveren en het afvoeren van materiaal.’
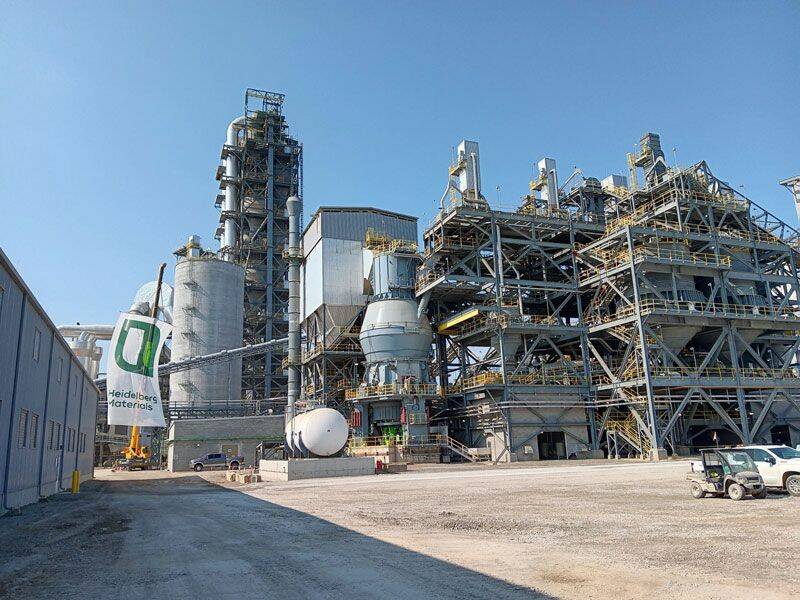
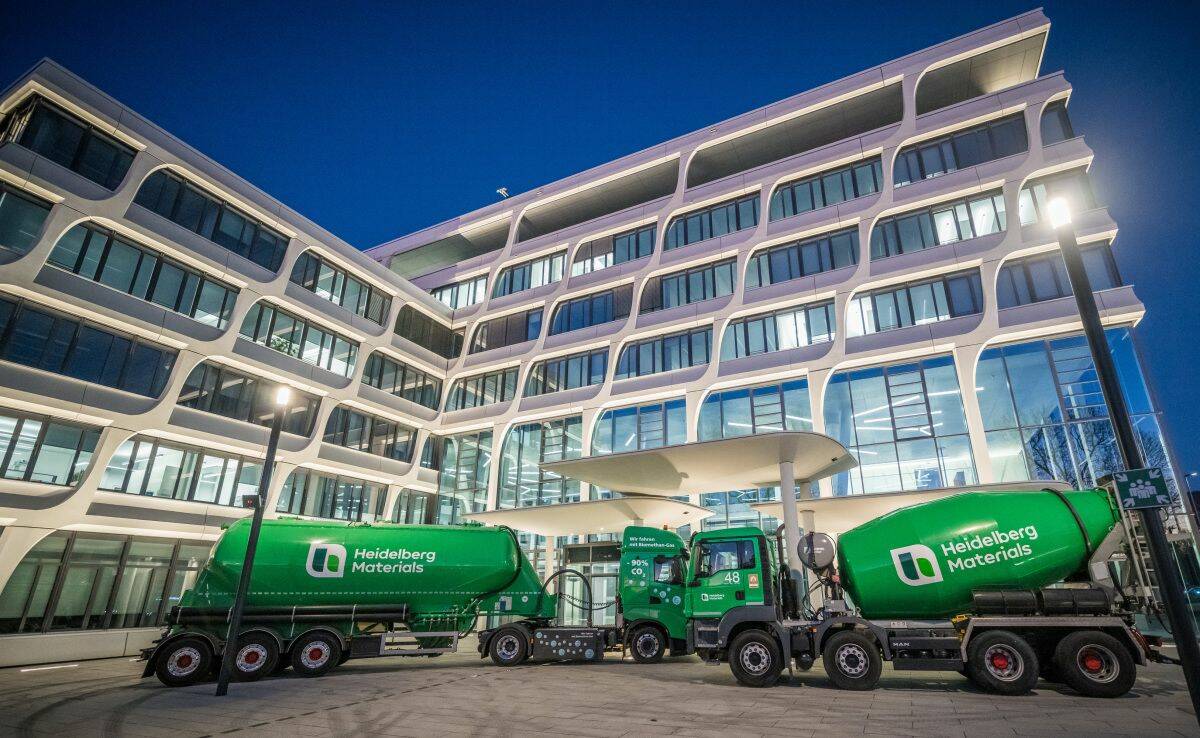
HOE ZORG JE ER DAGELIJKS VOOR MET JE TEAM DAT DE PRODUCTIEDOELEN WORDEN BEHAALD?
ENCI streeft ernaar om wekelijks voldoende cement te produceren om aan de vraag te voldoen. De productiedoelen zijn afhankelijk van de verzending die plaatsvindt. Hoewel de bouwsector momenteel wat vertraagd is, maakt ENCI nog steeds voldoende cement voor verschillende toepassingen zoals wegenbouw en tunnels. Ed: ‘We hebben hier twaalf silo’s staan, een voorraad van ca. 14.000 ton en het is de bedoeling dat iedere week de silo's vol zijn voor de week erna. Onze productiedoelstellingen zijn geheel afhankelijk van de verzending die per week plaatsvindt. Ik heb ‘s morgensvroeg overleg met de assistent productie en de technische dienst. Dan kijken we naar wat er aan storingen is gemeld en daarna ga ik of de assistent de controlekamer in en bespreken we met de collega’s de productie voor die dag. De teamcoördinator bepaalt wie waar welke werkzaamheden gaat doen. Dat is elke dag weer anders. Beginnende operators zitten vaak op dezelfde plek, omdat ze het werk daar eerst moeten leren, maar allround operators kun je overal tegenkomen.’
Ed begon bij ENCI als leerling operator en groeide door in de organisatie tot allround operator en teamcoördinator, sinds vorig jaar februari is hij productiemanager. ‘Het proces is niet heel ingewikkeld, er komen wel veel werkzaamheden bij kijken die allemaal worden uitgevoerd door onze operators. Dat is nou precies wat ons proces zo interessant maakt.’ We duiken met Ed in de wereld van cement en praten over wat er allemaal komt kijken bij het productieproces.
Ed Vergunst (54) is sinds 2015 werkzaam bij de Eerste Nederlandse Cement Industrie (ENCI), een bedrijf dat onderdeel is van de Duitse multinational Heidelberg Materials. Met twee producerende fabrieken in Rotterdam en IJmuiden speelt ENCI een belangrijke rol in de cementindustrie. Ed begon zijn carrière als leerling operator en groeide door tot productiemanager, waarbij hij verantwoordelijk is voor het leveren van hoogwaardige cementproducten.