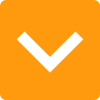
Bij Scania Production Meppel, één van de modernste lakinstallaties van Europa, werken ongeveer 700 medewerkers. Stefan Smit, head of maintenance, facilities & business continuity, deelt zijn enthousiasme over het Zweedse bedrijf. ‘Continu verbeteren zit echt in ons DNA. We willen elke dag beter worden dan de dag ervoor. Dit uit zich niet alleen in de ontwikkeling van betere producten, maar ook in het verbeteren van de planeet. Dat in combinatie met onze informele cultuur en de platte organisatie die we zijn, maakt dat we één familie zijn met elkaar.’
'CONTINU VERBETEREN ZIT IN ONS DNA'
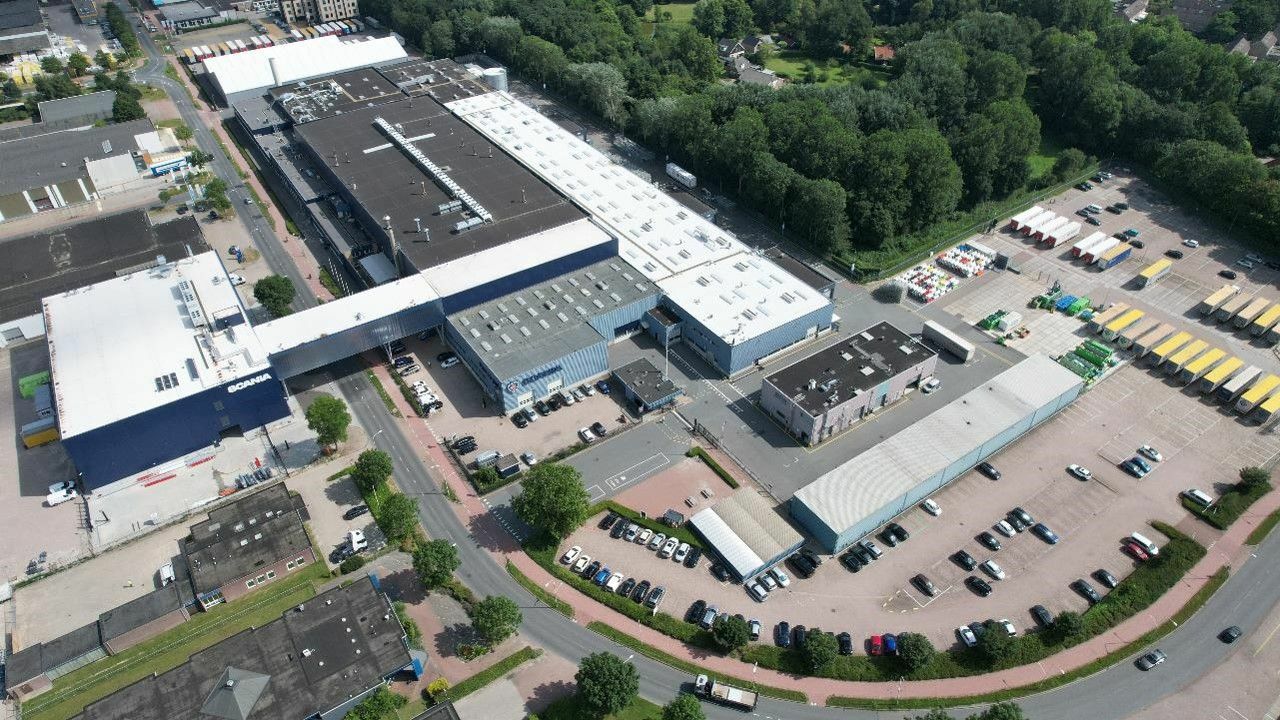
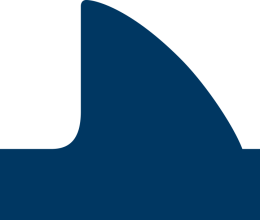
LEES OOK DE ANDERE VERHALEN VAN DE PRODUCTIE SECTOR
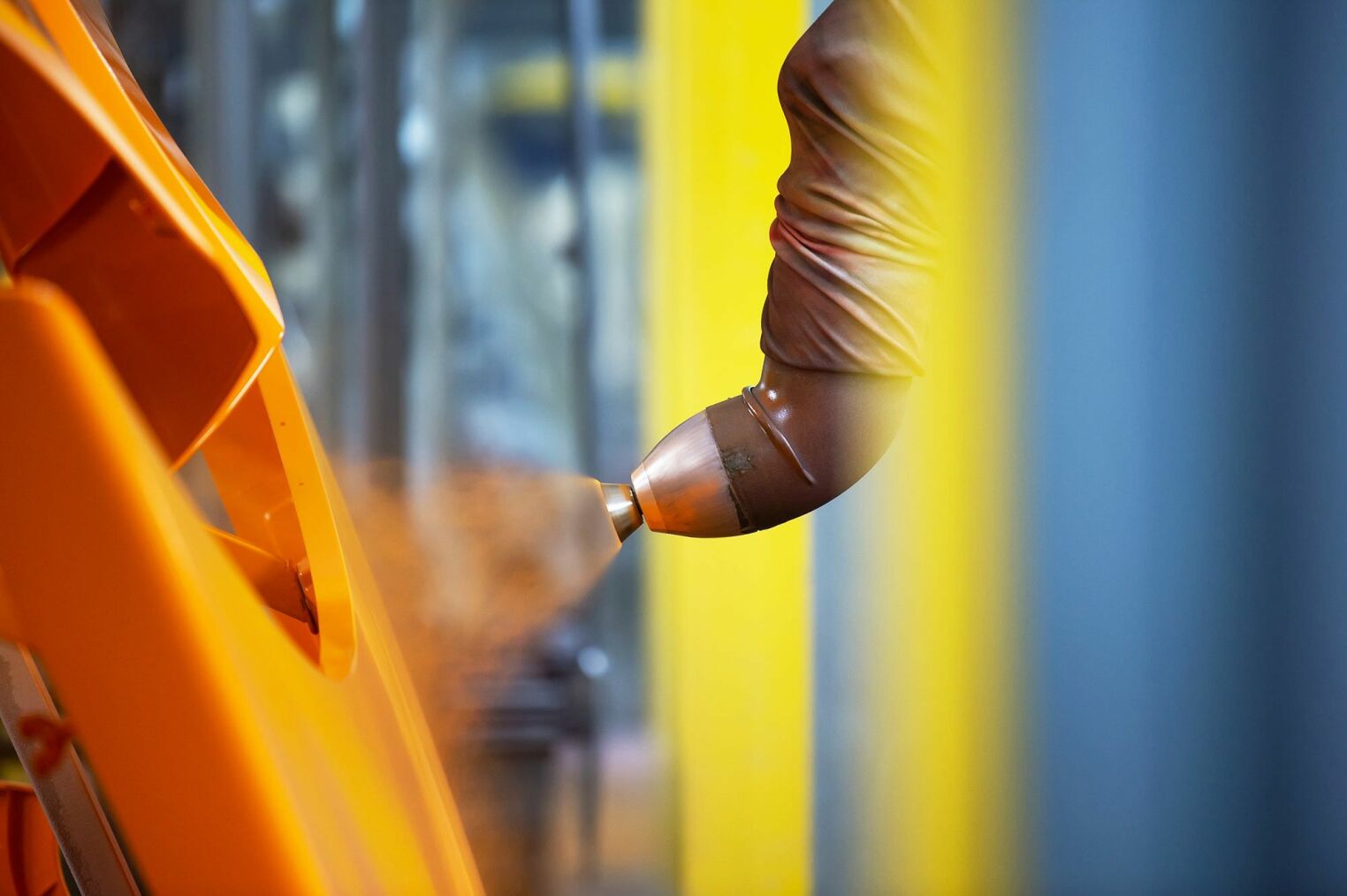
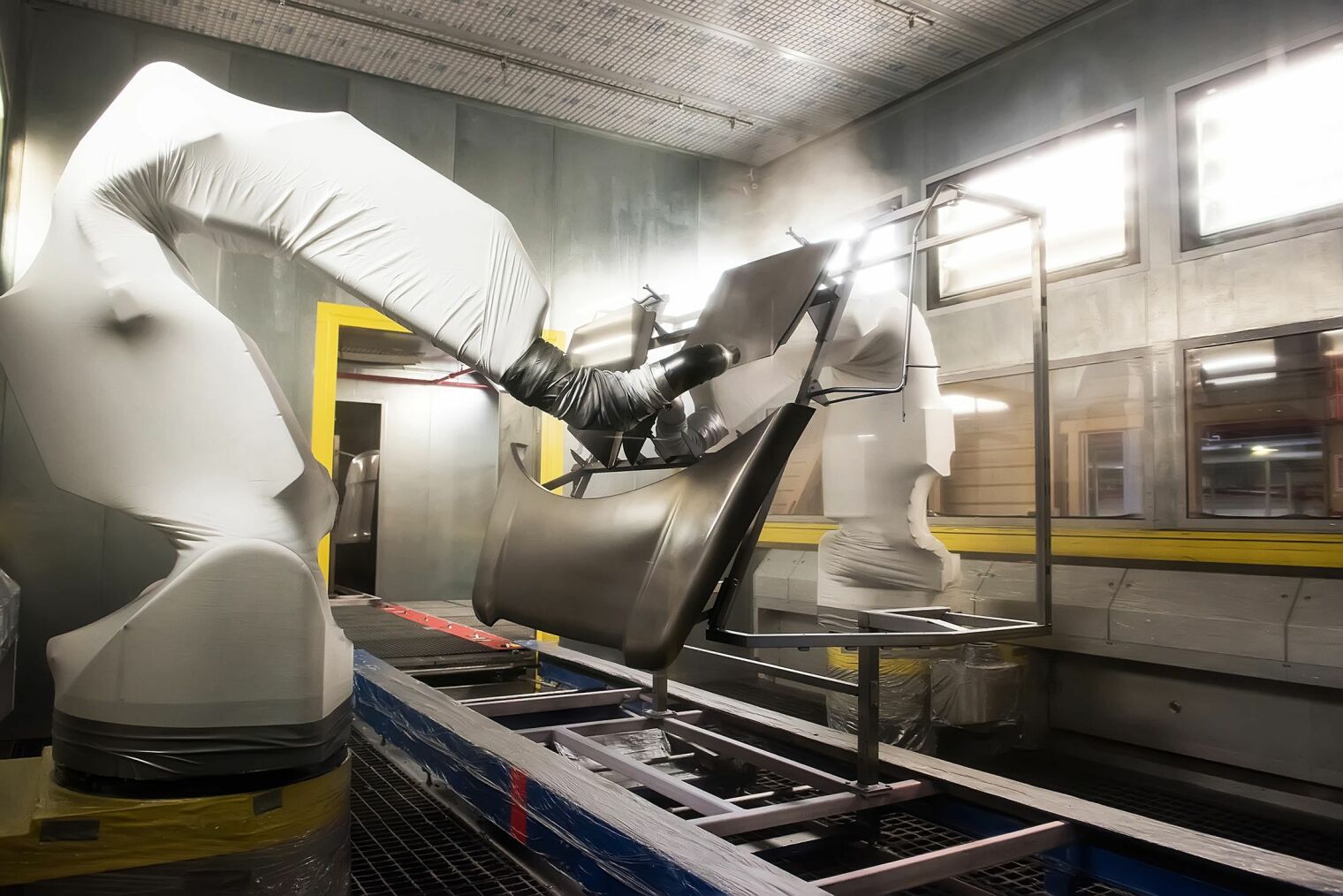
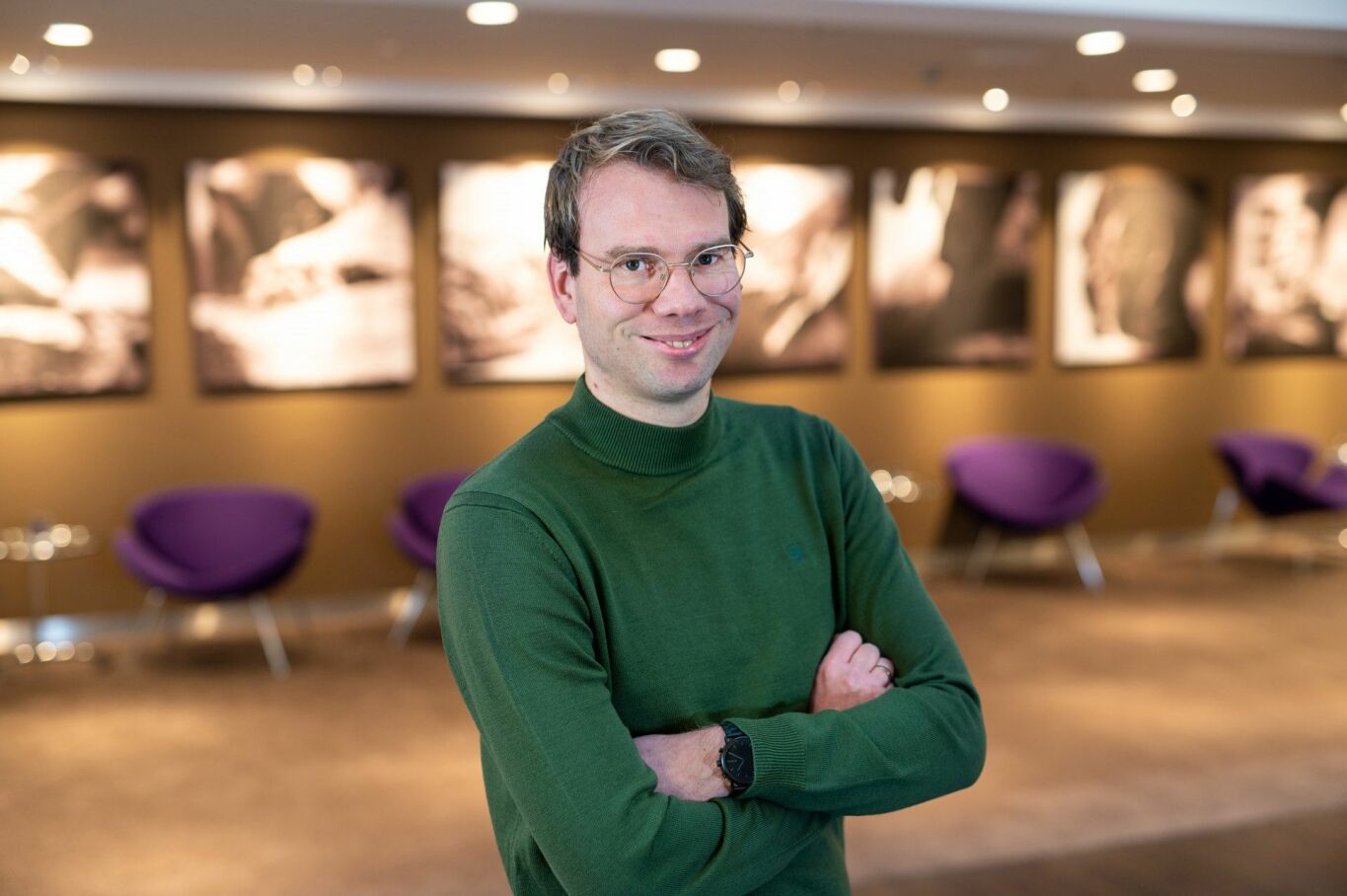
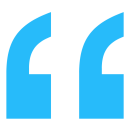
We zijn één familie met elkaar.”
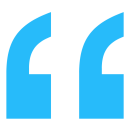
Hier komen diverse technische disciplines samen,
waaronder besturingstechnologie, robotica, werktuigbouwkunde en elektrotechniek.”
ONTWIKKELMOGELIJKHEDEN
Op de vraag welke interessante vraagstukken er bij Scania Production Meppel spelen, antwoordt Stefan enthousiast: ‘Hier komen diverse technische disciplines samen, waaronder besturingstechnologie, robotica, werktuigbouwkunde en elektrotechniek.’
Stefan legt vervolgens uit dat je als engineer bij Scania persoonlijke groei kunt doormaken. ‘Het begint bij het oplossen van kleine vraagstukken, en geleidelijk aan ga je steeds complexere en grotere projecten doen. Bovendien zijn er talrijke kansen voor doorgroei naar leidinggevende posities, zowel binnen de productie als extern. We bieden ook mogelijkheden voor uitwisseling, zoals naar Zweden gaan om daar als engineer werkzaam te zijn.’
JONG TALENT
Deze complexe vraagstukken vormen een significante uitdaging en vragen niet alleen om nauwe samenwerking, maar ook om specialistische kennis. ‘De engineeringafdeling die dergelijke projecten initieert, roept kennis in van diverse afdelingen. Ook onze expertise op gebied van onderhoud wordt hierin gevraagd,’ zegt Stefan. Hoewel er bij Scania veel getalenteerde medewerkers rondlopen, dwingen de uitdagingen waarmee ze geconfronteerd worden hen toch om meer talentvolle mensen aan trekken. ‘De behoefte concentreert zich vooral op technische kennis, essentieel voor het succesvol uitvoeren van projecten en voor het begrijpen van processen zoals lakken, machineonderhoud, en het beheersen van verwarmings- en koelingssystemen.’
DUURZAAMHEID
Als onderdeel van de bedrijfsstrategie van Scania zijn drie prioriteitsgebieden vastgesteld om in de toekomst duurzaam actief te kunnen blijven: CO2-armer, circulair ondernemen en duurzamer gebruik door de mensen die er werken. Stefan legt uit: ‘We onderzoeken bijvoorbeeld hoe we met de inzet van nieuwe robots het verbruik van lak en spoelmiddelen kunnen verminderen. Daarnaast richten we ons op het verduurzamen van de verwarmings- en koelsystemen in de fabriek. En we streven ernaar om voor 2035 in Meppel onze huidige gasgestookte systemen, die aan het eind van hun levensduur zijn, te hebben vervangen voor geëlektrificeerde alternatieven.’
LESSONS LEARNED
In 2022 is een nieuwe productiehal in gebruik genomen waarmee nu alle onderdelen in de primer (grondlak) kunnen worden gezet. Stefan over de opgedane kennis tijdens deze uitbreiding: ‘We hebben onze eisen en wensen heel nauwkeurig op papier gezet, om met onze leveranciers in gesprek te gaan en helder te kunnen communiceren wat we nodig hadden. Deze kennis passen we nu toe in het vervangingsproces. Daarnaast wisselen we binnen Scania kennis uit met teams die soortgelijke projecten hebben uitgevoerd, om van hun ervaringen te leren. Als onderdeel van de Volkswagen Group zoeken we ook de samenwerking op met andere entiteiten binnen de groep die zich bezighouden met lakprocessen, om lessen te trekken uit hun projecten.’
VERVANGINGSOPERATIE
In een periode van vier weken moeten de robots worden vervangen, een aanzienlijke onderneming. ‘Momenteel beschikken we over 30 robots, waarvan 22 vervangen dienen te worden en dat kan uitsluitend tijdens de zomerstop uitgevoerd worden. Dan hebben we vier weken de tijd niet alleen voor onderhoud, maar ook om vervangingswerkzaamheden te verrichten. Gezien de complexiteit van de machines, die zowel geïnstalleerd als getest moeten worden binnen deze krappe tijdslimiet, staan we voor een grote uitdaging. Tegelijkertijd streven we naar een minimale verstoring tijdens het opstartproces, want het proces moet wel blijven lopen zodra de machines operationeel zijn.’
UITDAGINGEN
De lakkerij is begin 2007 in gebruik genomen. Het plannen van het machineonderhoud maakt inmiddels plaats voor het vervangen ervan. Stefan legt uit: ‘We staan voor een aantal uitdagingen. De robots die destijds zijn geïnstalleerd, zijn aan vervanging toe. We zijn bezig met een stapsgewijs vervangingsplan voor de komende jaren. Ook andere machines naderen het einde van hun levenscyclus. Ons doel is niet simpelweg een machine vervangen door een soortgelijke machine, maar we kijken vooral of er verbetering mogelijk is, in de vorm van duurzame of energiezuinigere alternatieven.’
OVER SCANIA
Scania Production Meppel is specialist in het lakken van kunststof cabine- en chassisonderdelen. Stefan is als maintenance manager verantwoordelijk voor het onderhoud van de gebouwen, terreinen en installaties. ‘In Meppel lakken we de kunststof onderdelen die op de vrachtwagens zitten, die worden geleverd aan de Europese truckfabrieken van Scania in Zwolle, Angers (Frankrijk) en Södertälje (Zweden). Dit lakproces wordt volautomatisch uitgevoerd door dertig robots volgens de nieuwste technologie.’
LOOPBAAN
Twaalf jaar geleden begon Stefan als maintenance engineer bij Scania. ‘Ondertussen groeide het bedrijf en ben ik van maintenance engineer doorgegroeid tot groupleader maintenance office’, legt Stefan uit. Uiteindelijk nam hij de leiding over de gehele onderhoudsafdeling als head of maintenance, facilities & business continuity, een rol waarin hij een divers team aanstuurt, bestaande uit achttien eigen storing- en onderhoudsmonteurs, control systems engineers die de PLC’s onderhouden en programmeren, werkvoorbereiders, maintenance engineers en een groep verantwoordelijk voor facilities.
Stefan Smit
Maintenance Manager (MT) bij Scania
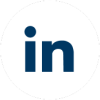
'CONTINU VERBETEREN ZIT IN ONS DNA'
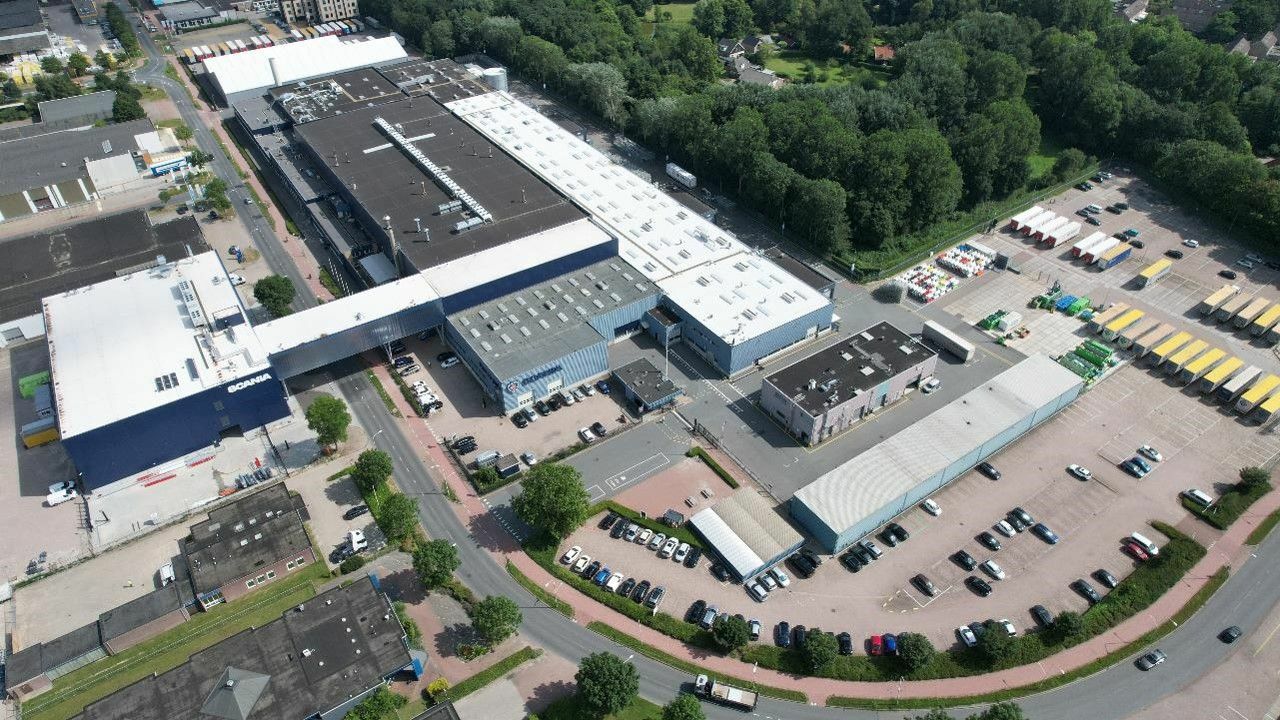
ONTWIKKELMOGELIJKHEDEN
Op de vraag welke interessante vraagstukken er bij Scania Production Meppel spelen, antwoordt Stefan enthousiast: ‘Hier komen diverse technische disciplines samen, waaronder besturingstechnologie, robotica, werktuigbouwkunde en elektrotechniek.’
Stefan legt vervolgens uit dat je als engineer bij Scania persoonlijke groei kunt doormaken. ‘Het begint bij het oplossen van kleine vraagstukken, en geleidelijk aan ga je steeds complexere en grotere projecten doen. Bovendien zijn er talrijke kansen voor doorgroei naar leidinggevende posities, zowel binnen de productie als extern. We bieden ook mogelijkheden voor uitwisseling, zoals naar Zweden gaan om daar als engineer werkzaam te zijn.’
JONG TALENT
Deze complexe vraagstukken vormen een significante uitdaging en vragen niet alleen om nauwe samenwerking, maar ook om specialistische kennis. ‘De engineeringafdeling die dergelijke projecten initieert, roept kennis in van diverse afdelingen. Ook onze expertise op gebied van onderhoud wordt hierin gevraagd,’ zegt Stefan. Hoewel er bij Scania veel getalenteerde medewerkers rondlopen, dwingen de uitdagingen waarmee ze geconfronteerd worden hen toch om meer talentvolle mensen aan trekken. ‘De behoefte concentreert zich vooral op technische kennis, essentieel voor het succesvol uitvoeren van projecten en voor het begrijpen van processen zoals lakken, machineonderhoud, en het beheersen van verwarmings- en koelingssystemen.’
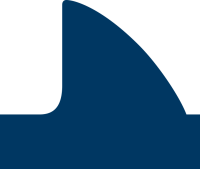
LEES OOK
DE ANDERE VERHALEN VAN DE PRODUCTIE SECTOR
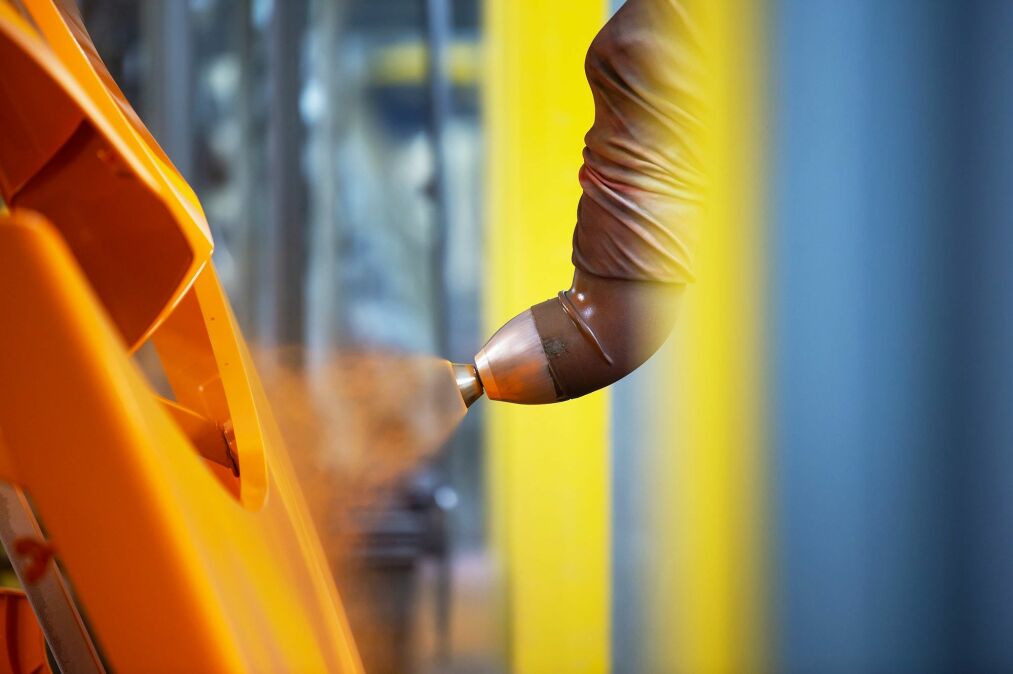
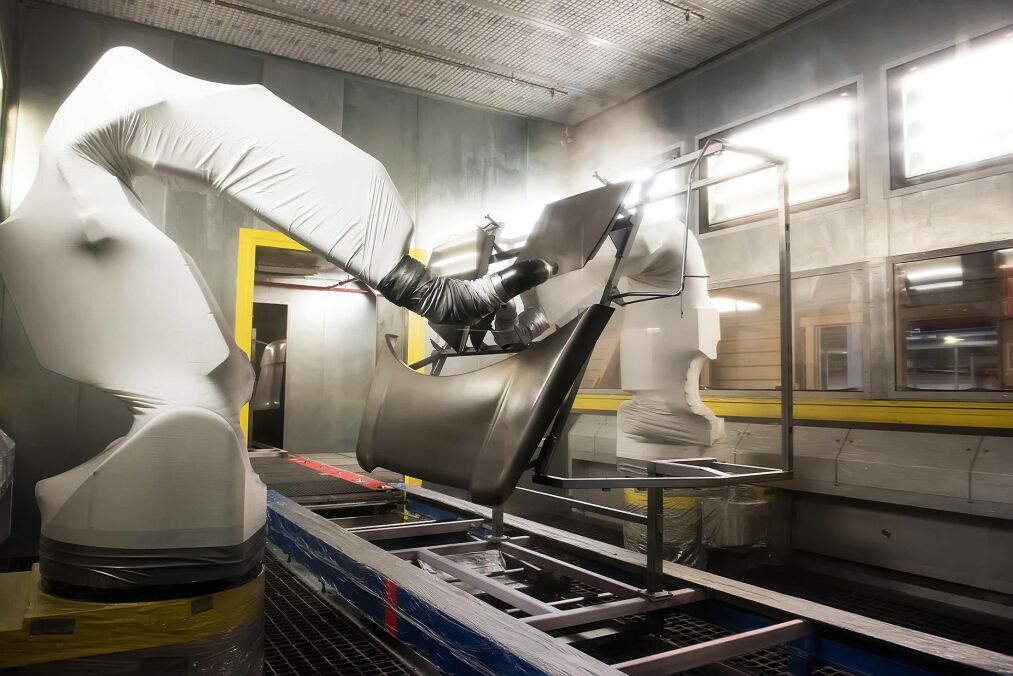
DUURZAAMHEID
Als onderdeel van de bedrijfsstrategie van Scania zijn drie prioriteitsgebieden vastgesteld om in de toekomst duurzaam actief te kunnen blijven: CO2-armer, circulair ondernemen en duurzamer gebruik door de mensen die er werken. Stefan legt uit: ‘We onderzoeken bijvoorbeeld hoe we met de inzet van nieuwe robots het verbruik van lak en spoelmiddelen kunnen verminderen. Daarnaast richten we ons op het verduurzamen van de verwarmings- en koelsystemen in de fabriek. En we streven ernaar om voor 2035 in Meppel onze huidige gasgestookte systemen, die aan het eind van hun levensduur zijn, te hebben vervangen voor geëlektrificeerde alternatieven.’
LESSONS LEARNED
In 2022 is een nieuwe productiehal in gebruik genomen waarmee nu alle onderdelen in de primer (grondlak) kunnen worden gezet. Stefan over de opgedane kennis tijdens deze uitbreiding: ‘We hebben onze eisen en wensen heel nauwkeurig op papier gezet, om met onze leveranciers in gesprek te gaan en helder te kunnen communiceren wat we nodig hadden. Deze kennis passen we nu toe in het vervangingsproces. Daarnaast wisselen we binnen Scania kennis uit met teams die soortgelijke projecten hebben uitgevoerd, om van hun ervaringen te leren. Als onderdeel van de Volkswagen Group zoeken we ook de samenwerking op met andere entiteiten binnen de groep die zich bezighouden met lakprocessen, om lessen te trekken uit hun projecten.’

Hier komen diverse technische disciplines samen, waaronder besturingstechnologie, robotica, werktuigbouwkunde en elektrotechniek.”
VERVANGINGSOPERATIE
In een periode van vier weken moeten de robots worden vervangen, een aanzienlijke onderneming. ‘Momenteel beschikken we over 30 robots, waarvan 22 vervangen dienen te worden en dat kan uitsluitend tijdens de zomerstop uitgevoerd worden. Dan hebben we vier weken de tijd niet alleen voor onderhoud, maar ook om vervangingswerkzaamheden te verrichten. Gezien de complexiteit van de machines, die zowel geïnstalleerd als getest moeten worden binnen deze krappe tijdslimiet, staan we voor een grote uitdaging. Tegelijkertijd streven we naar een minimale verstoring tijdens het opstartproces, want het proces moet wel blijven lopen zodra de machines operationeel zijn.’
UITDAGINGEN
De lakkerij is begin 2007 in gebruik genomen. Het plannen van het machineonderhoud maakt inmiddels plaats voor het vervangen ervan. Stefan legt uit: ‘We staan voor een aantal uitdagingen. De robots die destijds zijn geïnstalleerd, zijn aan vervanging toe. We zijn bezig met een stapsgewijs vervangingsplan voor de komende jaren. Ook andere machines naderen het einde van hun levenscyclus. Ons doel is niet simpelweg een machine vervangen door een soortgelijke machine, maar we kijken vooral of er verbetering mogelijk is, in de vorm van duurzame of energiezuinigere alternatieven.’
OVER SCANIA
Scania Production Meppel is specialist in het lakken van kunststof cabine- en chassisonderdelen. Stefan is als maintenance manager verantwoordelijk voor het onderhoud van de gebouwen, terreinen en installaties. ‘In Meppel lakken we de kunststof onderdelen die op de vrachtwagens zitten, die worden geleverd aan de Europese truckfabrieken van Scania in Zwolle, Angers (Frankrijk) en Södertälje (Zweden). Dit lakproces wordt volautomatisch uitgevoerd door dertig robots volgens de nieuwste technologie.’
LOOPBAAN
Twaalf jaar geleden begon Stefan als maintenance engineer bij Scania. ‘Ondertussen groeide het bedrijf en ben ik van maintenance engineer doorgegroeid tot groupleader maintenance office’, legt Stefan uit. Uiteindelijk nam hij de leiding over de gehele onderhoudsafdeling als head of maintenance, facilities & business continuity, een rol waarin hij een divers team aanstuurt, bestaande uit achttien eigen storing- en onderhoudsmonteurs, control systems engineers die de PLC’s onderhouden en programmeren, werkvoorbereiders, maintenance engineers en een groep verantwoordelijk voor facilities.

We zijn één familie met elkaar.”
Bij Scania Production Meppel, één van de modernste lakinstallaties van Europa, werken ongeveer 700 medewerkers. Stefan Smit, head of maintenance, facilities & business continuity, deelt zijn enthousiasme over het Zweedse bedrijf. ‘Continu verbeteren zit echt in ons DNA. We willen elke dag beter worden dan de dag ervoor. Dit uit zich niet alleen in de ontwikkeling van betere producten, maar ook in het verbeteren van de planeet. Dat in combinatie met onze informele cultuur en de platte organisatie die we zijn, maakt dat we één familie zijn met elkaar.’
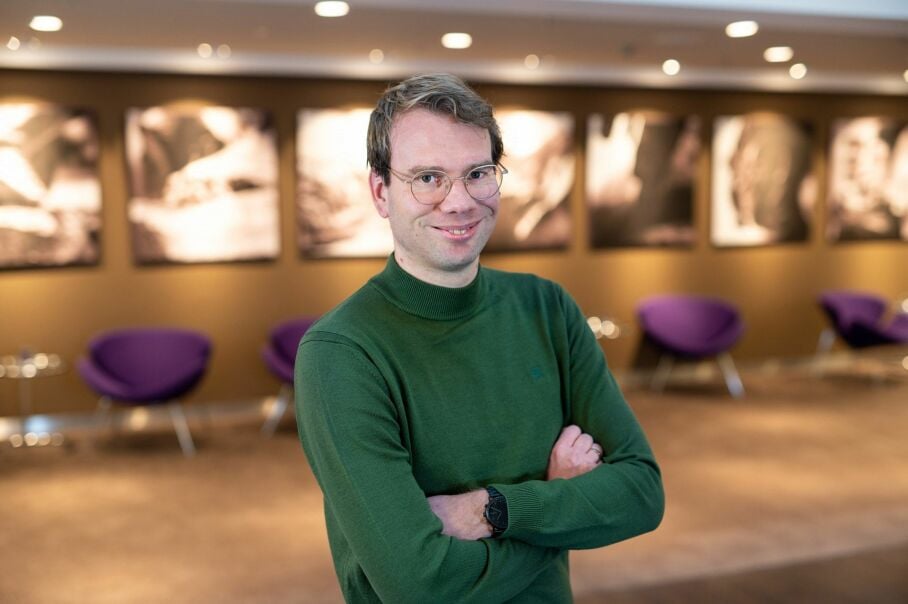
Stefan Smit
Maintenance Manager
(MT) bij Scania
